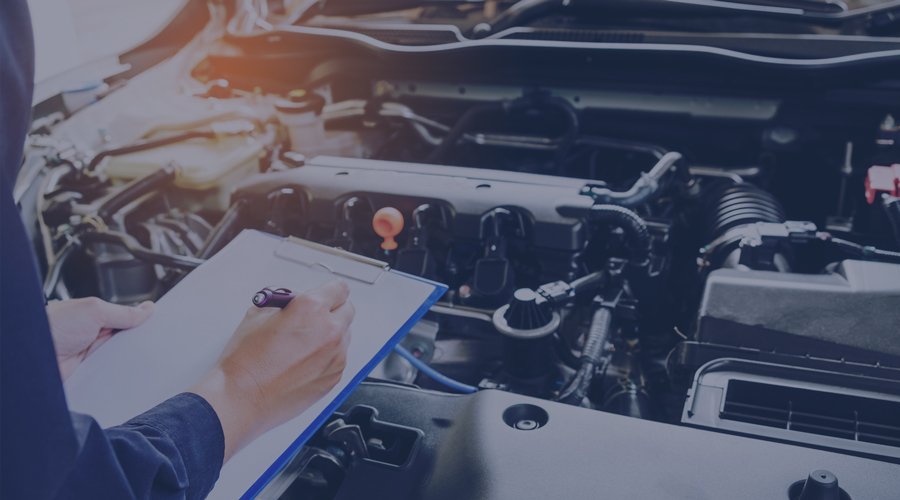
As Benjamin Franklin said, “failing to prepare is preparing to fail.”
When you’re running a service-based business, your ability to get the job done and maintain a good reputation depends on the reliability of your fleet.
Because of this non-stop dependence on fleet vehicles, it’s tempting to wait for an issue to come up before removing vehicles from the rotation to book them in for a service. Waiting for something to go wrong with your fleet vehicles is called ‘reactive maintenance,’ and it can be incredibly disruptive and costly.
In this blog, we’ll explain fleet maintenance strategy including what reactive maintenance is and the cost for small businesses. We’ll also talk about other maintenance strategies and how they can help you maintain your fleet.
What are the different types of maintenance strategies?
There are two major maintenance philosophies:
- Reactive maintenance
- Preventive maintenance
Each can be broken down into a few subcategories based on their nuances.
What is reactive maintenance?
Reactive maintenance is sometimes called ‘breakdown maintenance’ because it refers to repairs that are done to vehicles after something has already broken down.
In short, it means waiting for something to break before you fix it.
What are the cost implications of reactive maintenance?
Relying on reactive maintenance may be tempting because it means less time is spent planning vehicle maintenance schedules for your fleet, but reactive maintenance is ultimately a shortsighted strategy that can lead to expensive issues down the road.
Waiting for something to break down guarantees that there will be unscheduled downtime because of unplanned repairs. Breakdown fixes can also cost more than routine preventive maintenance thanks to factors like rushed part costs and revenue lost due to canceled service visits. It may also lead to a dangerous situation for yourself and your employees.
Whoever said “if it ain’t broke, don’t fix it” didn’t spend a lot of time monitoring their bank account.
What is an example of reactive maintenance?
It’s late spring and a pool company’s schedule is fully booked as their customers prepare for summer. One vehicle has had a warning light on the dashboard for a few weeks, but the driver keeps forgetting to notify their manager.
At the start of another busy day, the vehicle won’t start and has to go into the shop for repairs. Because it’s unscheduled breakdown maintenance, the service department doesn’t have the parts so it won’t be ready for two weeks.
The unfortunate outcomes of reactive maintenance
By relying on reactive maintenance, the company ends up needing to postpone several jobs, resulting in unhappy customers, unfinished work, and lost revenue.
Because they used a reactive maintenance strategy and didn’t have a maintenance schedule or a tool to monitor DTC (Diagnostic Trouble Codes), the business now faces unexpected expenses, unplanned downtime during the busiest part of the year, and damage to their reputation.
What is preventive maintenance?
Preventive vehicle maintenance is a proactive approach that uses routine maintenance to minimize repair costs and unscheduled breakdowns in the long term.
What is the difference between preventive maintenance and reactive maintenance?
With a proactive maintenance strategy, it’s all about looking for clues to foresee equipment issues and addressing them before they result in equipment failure.
Whereas, reactive maintenance is sort of like crossing your fingers, hoping for the best, and dealing with issues when they arise—not the best approach when it comes to maintenance strategies or minimizing repair costs.
How does preventive maintenance work?
With preventive maintenance, maintenance is scheduled at predetermined times, or according to prescribed criteria. The goal of a proactive or preventive maintenance strategy is to ensure that you don’t incur unnecessary repair costs, leave customers unserviced, jobs unfinished, or leave your employees stranded. It also keeps vehicles in action longer because they’re regularly serviced, preventing breakdowns that threaten to derail operations.
Preventive maintenance is often called planned maintenance because planning out a service schedule is central to successful preventive maintenance. With this approach, maintenance cycles are planned according to the need to take vehicles out of service rotation, so that business can continue as usual with minimal disruption.
By reducing the risk of failure and performance degradation of the vehicle, small business owners can prevent revenue loss and surprises that leave them scrambling to reschedule work on short notice.
What is an example of preventive maintenance?
It’s getting warmer and the schedule is filling up for a local HVAC company. The business is swamped and booked out for the next two months by folks looking to get their air conditioning units ready for the summer.
Because the HVAC company knows that this is the busiest time of the year for business, the business owner made the decision to schedule maintenance for the fleet a few weeks before things kicked off to make sure vehicles were in good condition throughout the rush. Thanks to their rotating schedule, there’s no lapse in service delivery as vehicles are pulled from service one-by-one. The business was also able to budget for this cost at the start of the year, so it’s not an unexpected expense.
While one of the vehicles is in the shop, the repair team notices that the brake pads are dangerously deteriorated and that there was a recent recall on the driver-side air bag, which they manage to fix—preventing a potentially very dangerous and expensive issue during the busy season.
The beneficial outcomes of preventive maintenance
Preventive maintenance essentially means preventing fires instead of putting them out. By regularly performing maintenance checks to keep a vehicle in good shape, you can prevent unplanned breakdowns, ultimately improving fleet reliability, reducing downtime for your small business, and better resource planning all year long.
What is corrective maintenance?
Corrective maintenance is a maintenance program that’s not quite preventive, but more effective than reactive maintenance.
This is when you fix something that is still technically operational, but a small issue has appeared.
The goal of corrective maintenance is to restore the vehicle to normal operating condition before something goes really wrong and you’re forced to make emergency repairs.
What is the difference between reactive and corrective maintenance?
Corrective maintenance happens in situations like when a vehicle will still drive, but there’s a strange noise. It still works, but it might become unsafe soon.
Reactive maintenance is when you wait for the vehicle to become completely unusable before you take it in for repairs.
Corrective maintenance in action
The manager of a plumbing company is notified that two vehicles have new DTC codes on the dashboard. He books them in for servicing later that same week.
He rearranges the schedule so the team can still cover most of the work they had planned. He still has to push one job out, but he’s able to notify the customer early, maintaining the relationship.
The outcomes of a corrective approach
In this situation, the business is able to make things work, but they still have to make stressful adjustments on the fly.
Also, if they were relying on the drivers and technicians to notify them about alerts, there’s no way to know for sure how long the error has been there and how long it’s safe to wait before taking the vehicle off the road.
How to keep your fleet reliable with corrective maintenance
This practice is only as reliable as the information available. When relying on driver memory, there is automatically a margin of human error, and that margin for error only grows as your business grows.
Corrective maintenance becomes a much more dependable practice if you’re using a tool to automatically monitor your fleet’s health.
Moving beyond a reactive maintenance strategy
At the end of the day, reactive maintenance will always be an inescapable factor in keeping any small business fleet up and running. There will always be surprises, like collisions or rock-inflicted damage—but it shouldn’t be the only maintenance strategy for businesses that rely on their fleet to get the job done.
While it certainly takes less time spent planning to rely on reactive maintenance, the costs when something does go wrong can be devastating. With reactive maintenance, businesses end up paying for more than just a repair. There’s also the resulting revenue loss, costs of rush orders, and potentially irreparable damage to your business’s reputation.
Whether you decide to plan your maintenance schedule out months in advance, or depend on a corrective program to keep your business running, your fleet maintenance program will only work if you know what’s wrong, and when it went wrong.
Better fleet maintenance for small businesses
Fleet tracking and vehicle health monitoring technology like Force Fleet Tracking helps take the planning out of preventive maintenance and reduces reactive maintenance. With fleet vehicle health and maintenance software, small business owners monitor their fleet vehicle status by flagging recalls, fuel and battery levels, predictive maintenance alerts, and DTC codes in plain English. There’s no intensive installation, so you can spend more time finishing the job.
Because when it comes down to it, preventive maintenance is about more than your fleet—it’s about maintaining your business.
Try Force for free and start minimizing unnecessary downtimes.